In industrial automation and material handling, the selection of screw conveyors directly impacts production efficiency and operational costs. This article analyzes the core differences among stainless steel, carbon steel, and flexible screw conveyors from a client perspective, helping you align with precise needs.
1. Material & Application Comparison
1. Stainless Steel Conveyors
Pros: High corrosion resistance (ideal for acidic/alkaline environments), sanitary compliance (FDA/GMP certified), lifespan >15 years.
Cons: Higher cost (30%~50% pricier than carbon steel), unsuitable for ultra-heavy materials.
Typical Use: Food processing (e.g., flour transport), pharmaceutical raw material handling, corrosive powder transfer in chemical plants.
2. Carbon Steel Conveyors
Pros: Cost-effective (lowest upfront price), high structural strength (2-ton/m load capacity), heat resistance (<200°C).
Cons: Requires anti-rust maintenance (40% shorter lifespan in humid conditions), limited hygiene compliance.
Typical Use: Mining ore transport, construction material handling, grain storage in dry environments.
3. Flexible Screw Conveyors
Pros: Adaptable layout (30°~90° bend angles), rapid cleaning (5-minute disassembly), energy-efficient (40% lower consume than traditional models).
Cons: Short conveying distance (≤12 meters), incompatible with sharp/hard materials.
Typical Use: Plastic pellet mixing lines, cosmetic powder filling, multi-station feeding in labs.
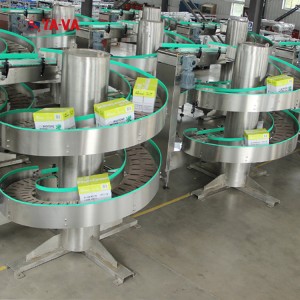
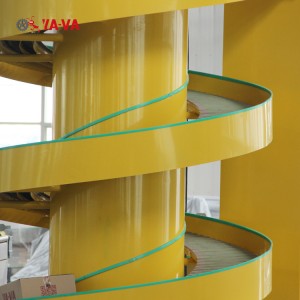
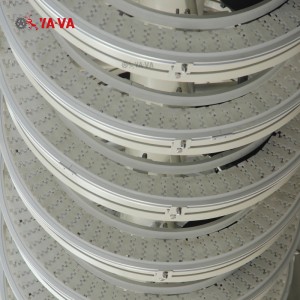
2. Three Critical Decision Factors
1. Cost Structure
Initial Investment: Carbon steel < Flexible (≈15,000) < Stainless steel (≈25,000).
Long-term Maintenance: Flexible conveyors have the lowest annual cost (~1,200/year), stainless steel depends on cleaning frequency.
2. Efficiency & Output
Capacity: Stainless/carbon steel models reach 50 m³/h (long-distance), flexible models max at 30 m³/h (short-distance).
Adaptability: Flexible conveyors reduce facility modification costs via multi-angle installation.
3. Compliance & Safety
Food-grade: Only stainless steel and flexible models meet FDA standards; carbon steel needs coatings (+20% cost).
Explosion-proof: Flexible models offer anti-static options (e.g., YA-VA series) for chemical dust environments.
3. Client Decision Flowchart
Material Type → Corrosive/Humid? → Yes → Choose Stainless/Flexible
↓ No
Conveying Distance >12m? → Yes → Choose Carbon/Stainless
↓ No
Need Flexible Layout? → Yes → Choose Flexible
↓ No
Budget Priority → Choose Carbon Steel
ConclusionSelecting a screw conveyor requires balancing the "cost-efficiency-compliance" triangle. Prioritize communication with suppliers about material properties and operational scenarios. Customized solutions like YA-VA series can further optimize total cost of ownership (TCO).
Post time: Feb-25-2025